|
Our optimization project: LT-heating system
- The data of the system 2001 renewed
- An overview of 17-years successful energy-saving in figures
- The outcome of optimizing
- Data from the house according to EnEV
- Deeper background information
- The old system from 1985-2001
The heating system (2) in words and pictures
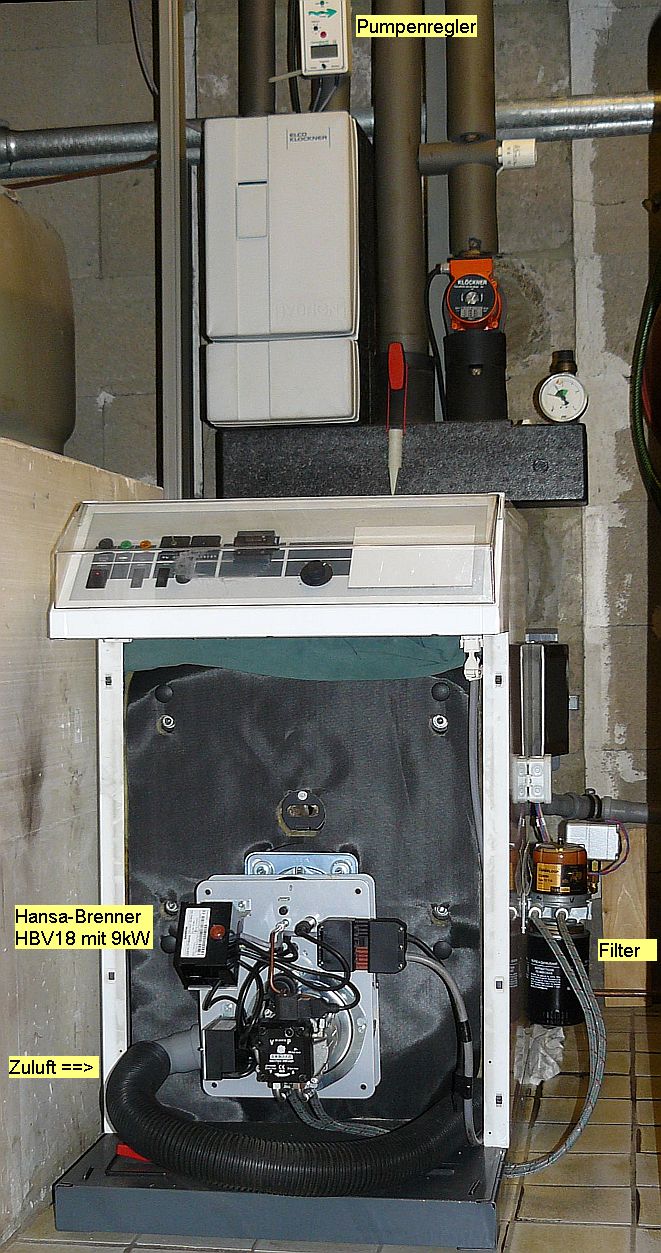
View of the system: Boiler and distribution pipes
with insulating material and cover removed. [Photos: db]
|
As you can see, we changed the boiler - it was more work than expected and we are not yet finished.
Thanks to the companies who supported us so helpfully in this project:
ELCO-Klöckner: Boiler and burner
Werner & Co: Filter and oil atomizer
Technaflon: Off-gas pipe made of teflon
- And all those who helped with good ideas and useful parts...
The entire pipe system was refitted and a silencer was inserted in the off-gas pipe because the blue-light burner is more noisy. The oil supply assembly was fitted with a Tiger-Loop containing a fine-mesh oil filter as used in cars. The filter achieves removal of gas from the oil. You only need one supply pipe even using a 2-pipes connection and the heat of the pre-heating is recycled.
Tiger-Loop with MANN-Filter cartridge 712
|
Nothing unusual on the outside - balancing the components is the key aspect: what you don't burn, you don't pay.
Tiger-Loop Filter
The effect of the tiger-loop filter which we particularly benefit from is that it achieves low power by reducing oil flow-through. This is what happens:
The filter design allows the preheated oil returning from the pump to run into the inlet. After 3 minutes, the temperature reaches about 30°C. The extra temperature increase from the preheater in front of the atomizer (approx. 55K) brings the temperature of the oil in the atomizer up to 80-90°C. The oil then has a viscosity of nearly 1.0 Centistokes (as fluid as water), which is optimum for excellent spraying properties. (Thanks to Mr. Bürgermeister for the tip!)
Because oil-atomizers respond to lower viscosities by reducing flow-through, we arrive at a 'pre-heating factor' of 0.866 in contrast to the normal pre-heating factor of 0.889 (Weishaupt). This means that with a 0.3 gallons atomizer you can reckon with a ~15% reduction in flow-through.
This is not absolutely perfect, because the burner then needs a three-minute warm-up time. So longer running-times are preferred.
We are passionate data gatherers
Assessing saving effects is only possible by annual comparisons. We have been collecting data from this heating system on an ongoing basis since 1994, and have approx. 24 MB of data recorded at 15-minute intervals. This allows us to reconstruct the status at any given moment.
We cannot quite understand why all manufacturers to whom we offered our data reacted by asking: "What shall we do with this data?"
[ Contents ]
Data of the system from 2001
- 'Systron Öko-Plus 2-22' multi-purpose low-temperature system with water heating.
- Controller Logon M (G+Z1) from Lamberti
- Air-Offgas-system for pre-heating burner air and to reduce off-gas loss.
- Off-gas pipe with silencer and Teflon off-gas pipe.
- Burner
- 'EK 01B.28 L-NH' light heating oil blue-flame burner
- Optimized output of the burner with Delavan atomizer 0.3/80°/8bar ~ 10kW. 12%CO2
- Oil counter with pre-filter.
- Tiger-Loop filter to reduce flow-through, de-foaming, elimination of air.
- 1 circuit of underfloor heating
- Distribution: Electro-mechanical mixing valve
- Electronic pump controller with dT-characteristic.
- Charge pump used as return-boost pump to protect the boiler.
- Hot water tank
- 'Bindl' (300 liter) hot water heating tank
- No circulation pump
History of changes
Before May 2001
As outlined in the section dealing with oil burners, it was not easy to get the new blue-burner EK 01.28L-NH to its minimum power output. It comes with an atomizer 0.45/80º and is adjusted to ~15 bar oil pressure, resulting in a combustion power of 22kW.
We solved electrical problems of the brand-new Lamberti-Controller: faulty contact in modules. A 3-hour job!
Thanks to Peter Gerlach without whose technical curiosity and persistence we wouldn't have got to this point.
December 2001
We connected the air-intake of the burner with a 55mm hose to the air-offgas-system of the chimney.
Fitting a 0.3/80º atomizer at 14.5 bar only achieved a 6% CO2 output, because the air adjustment was not accurate enough.
March 2002
Mixer was aligned to the atomizer: max. 12.6% CO2.
Fitted smaller mixer: no change in CO2.
Problems with blooming sulphur cause by the condensation at the muffler.
Experiments to reach the heating threshold.
May 2002
Planned a self-constructed air adjustment.
Up to August 2002
Mixer immovably rusted. Derusted and reassembled and smeared with silicon grease.
Air adjustment device of the burner adjusted, so that low burner power output is possible. burner adjusted to 8 bars, ~ 10kW. (Not good news for the German chimney sweep, one job less for him - so is Germany.)
Unfotunately onla 10,5% CO2, that means still too much air. We will change that next time. While adjusting, we noticed that the burner still runs when the oil pressure ist 6 bars and even stars under these conditions.
December 2003
Backflow booster pump installed:
Distributor valve installed behind the hot water charging pump and boiler back flow.
Installing the pump enables you to use the pump as
- backflow booster pump and
- hot water charging pump.
This requires a special but simple control.
This determines more need of electrical energy per year: 226kWh.
|
Twin-function backflow booster pump
|
May 2003
Oil meter with a pre-filter
|
Oil meter installed. You then see how inaccurate your figures were before. The oil meter shows that the hourly flow rate of oil is about 1.0388 liters = 10.47kW.
|
December 2003
Klöckner/Lamberti controller taken out of operation and a freely programmable JCI controller installed, which is currently being set to achieve a minimum number of burner switch-ons per day. The savings are already there because the device is running according to the outside/room temperature strategy. More data to come in 2004.
July 2004
Because inaccuracy in manufacture made the Elco burner leak when set to low power, the new, specially constructed air control didn't change much. The only remedy would be a better burner.
Checks give us the same result: an off-gas loss of only 2% (lower heating value), i.e. 98% burner efficiency. All this without substituting the existing low temperature boiler by a condensing boiler!
May 2006
Because the air setting of the Elco burner was unsatisfactory, we successfully replaced it with a Hansa HBV18. Nozzle: an individually measured Steinen 0.3/75° of 9.2 bars.
boiler temp. 45° (adjusted)
inflow temp. 32° (due to air/off-gas system)
off-gas temp. 67.5°
CO: 42ppm
|
O2: 4.2%
CO2: 12.2%
air excess: 1.25
off-gas loss: 1.8%
|
June 2006
Insulation is blown in
|
Reduction of heat losses, less air through non-visible joints, better sound insulation
|
Blowing in the insulation material was quick and no mess: the whole thing was finished in 3 hours.
Details about handling the off-gas
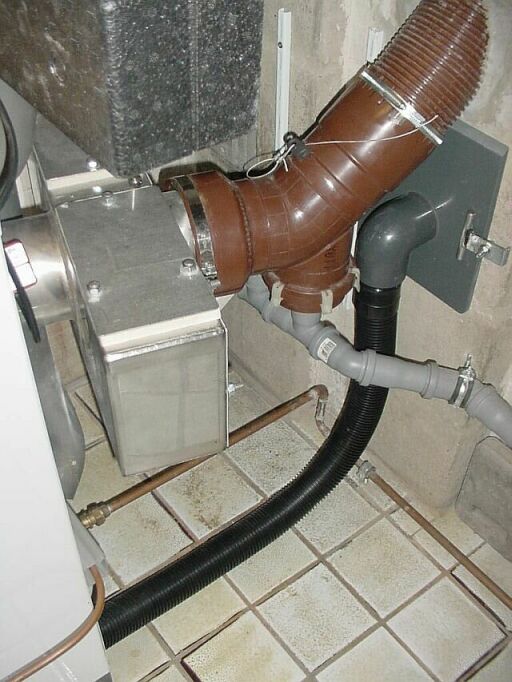
Silencer at the off-gas pipe, condensed water and suction pipes [Photo:db]
|
The flue gas temperature for this boiler is factory-set to 150ºC max. Actually, when heating water, in the core flow we measured up to 190ºC.
The boiler came with 2 turbulators installed. The flue gas temperature was a bit too high for the Technaflon pipe. So we inserted the 3 extra turbulators supplied, achieving an flue gas temperature of about 80ºC above boiler temperature. The previous figure was 150ºC. The smaller atomizer (0.3/80º) will achieve a further reduction to 120ºC.
By extending the suction path using the space running between the old chimney and the new pipe, the air incoming to the burner is preheated via heat exchange for about 24-30K. The advantage is that all condensation takes place exterior to the boiler, i.e. in the chimney. A pipe of this kind can be fitted to almost any boiler.
|
Special control and adjustment features
We didn't change what was working:
The combination of two sensors in the heating circuit forming one mean value is a tailor-made unit from Klöckner 1988 (thanks to Herr Pieck, because Klöckner had nothing like that in the standard range) this came out of an idea I got from Velta.
With underfloor heating the difference in temperature between inlet and outlet is directly proportional to power consumption, i.e. normally in the range 4.8K (in January) to 1.2K (May). These figures are operating mean values over the last 7 years. The greatest difference occurs mornings when heating up: ~10K (constant for 10 hours, measured 1.1.1997). During this time, recording Tin and Tout in order to calculate mean values has a big impact on room temperature. The rest of the day, mean value calculation results in a power-related increase in the inlet temperature equal to approx. half of the above-mentioned values.
|
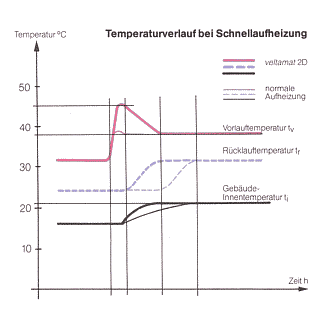
Ideal temperature graph [Source: Velta]
|
You can feel that the heat-up phase is shorter, which means that you can start heating up later.
Best effect of the new control are the savings of up to 40% in the summer/winter changeover period because of the option of being able to select the heating activation threshold.
[ Contents ]
An overview of successful energy-saving in figures
Year
|
Outside temp. 1w-min{°C}
|
No. degree days 15/20 {d*K}
|
Burner starts {#}
|
Burn time {h}
|
Oil used {kWh/m˛}
|
Actuation {kWh}
|
What we did
|
1990
|
|
3147
|
measurable
|
measurable
|
126.03
|
|
15/9: Switch-on & running time counters built in
|
1991
|
|
3540
|
13627
|
1781
|
132.36
|
|
|
1992
|
|
3291
|
10055
|
1473
|
133.85
|
|
Mean value for these 3 years is baseline for differences in values |
1993
|
|
3509
|
12011
|
2089
|
102.81
|
|
|
1994
|
|
3188
|
11070
|
1493
|
114.22
|
|
04/94 Data gathering unit built in
|
1995
|
-6.80
|
3811
|
6289
|
1677
|
111.25
|
|
Min. running time &
lower limit temp. changed
|
1996
|
-10.80
|
3948
|
3626
|
1918
|
109.10
|
|
Jan.: Atomizer of 0.3/60º etc..
|
1997
|
-15.40
|
3295
|
3274
|
1487.8
|
89.75
|
1350
|
Heating pump control & warm water vacation switch installed
|
1998
|
-5.51
|
3290
|
3749
|
1554.6
|
93.84
|
1138
|
Test: boiler cleaned, when waste gas >220ºC
|
1999
|
-4.51
|
3209.4
|
3234
|
1429
|
89.64
|
1066
|
(Jan.: This table created :-) long time off in summer
|
2000
|
-3.55
|
3049
|
2879
|
1340.4
|
89.52
|
1060
|
reducing the burners on/off
|
2001
|
-4.31
|
3337
|
5183
|
1132.7
|
82.02
|
1007
|
New system, new savings
|
2002
|
-5.06
|
3094
|
3756
|
1203,6
|
73.59
|
979.7
|
Heating threshhold 13º, fight with the new burner - power to ~10KW, ~45W/m²
|
2003
|
-7.90
|
3209
|
4135
|
1640.7
|
75.92
|
1206.3
|
12/02: backflow booster pump installed
|
2004
|
-4.88
|
3392
|
1970
|
1657.25
|
77.13
|
1254.3
|
Controller replaced by a JCI-DX. 3 months testing the backflow control.
|
2005
|
-6,15
|
3183
|
2129
|
1709.51
|
82.89
|
1275.5
|
Mehr Verbrauch, aber viel bessere Regelkonstanz Innentemperatur bei Kälte.
|
2006
|
-6,15
|
3183
|
2129
|
1709.51
|
77.03
|
1275.5
|
Summer 2006: new burner, wall insulation, new window glasses
|
Last 3 years' total mean
|
2004-06
|
-4.52
|
3230.33
|
1994.67
|
1611.57
|
79.02
|
1248.23
|
18.4% annual running time of burner
|
Savings in 2006, baseline 1991-1993
|
-84.2%
|
|
-39.6%
|
|
599.94 euros oil + 82.69 euro tax annually!
|
Key to the 10-years overview:
Temperatures & statistics |
These data have been logged by us since installing the data logger. The years before 1995 we relied on external data recording. To normalize consumption we use Aachen's official data of degree-days.
Click on an annual mean temperature to see a graph showing the statistical break-down of temperatures over the year in a new window.
|
Oil consumption kWh/m˛ |
The value is the climate-corrected consumption-to-surface ratio, the calculated mean requirement, normalized to a number of degree days over a 10-year period.
|
Actuation |
Since 1996, the electrical power required for the actuators is metered separately and includes control, pumps, the burner and data gathering (taking 70W * 24h * 365 days = 613,2 kWh ).
The final result normalized to the number of degree days is about ~4.8 kWh/m²*a, i.e. about 0.7 euro/m²*a.
|
Current status |
All figures are for one year, the current status is the 1.1.2007
|
[ Contents ]
The outcome of optimizing
With this standard boiler system we achieved a 35% reduction in 2004 compared to the mean consumption in 1991...1993. This calculation is normalized to the long-term 10-year mean value for the number of degree days.
This considerable reduction was achieved only by modifying the heating system, without structural modification to the house. Changing the boiler is not absolutely necessary, or in other words: Savings in oil consumption with no loss of comfort can be made, even with an old heating system. The essential optimization is fine-tuning the system to the user's requirements, otherwise you might just as well switch off :-)
The savings have been realized by consistent reduction of losses through rationalization of use, and adaptation of control and system components. The main losses are due to the heat generating and hot water distribution system components:
Heat generating
- Waste gas losses (which are about 10% always and everywhere)
- Cooling losses
- Combustion time and switch frequency
- Hot water availability losses
- maintenance!
Heat distribution
- Insulation
- Minimizing hot water circulation
[ Contents ]
The house data according to EnEV for 2002
Kind of energy required |
Total {kWh/a} |
Specific {kWh/m²*a} |
Primary energy factor |
Remarks |
Final energy (oil cons.) |
15710 |
70.8 |
1.46 |
normalized to no. deg. days |
1. Warm water heating |
2775 |
12.5 |
|
<=! to EnEV definition |
2. Heating requirement |
12935 |
58.27 |
|
Calculated as remainder |
3. Elektrical actuation power |
366.5 |
1.65 |
3.25 |
measured, excl. data logger |
Primary energy |
24127.73 |
108.68 |
|
Total, normalized to no. deg. days |
These data are valid at an A/V - factor of 0.74, heated area: 222m², fuel heating oil.
The total mean consumption of the house constructed in 1987, is 108.68 kWh/(m˛*a) - meets the German EnEV (Energy-Saving Regulation): 112.3 kWh/(m˛*a).
What are the real requirements for hot water ?
The warm summers of 1999 and 2003 meant that we didn't need to heat at all. This enabled us to measure the net cost of our hot water supply:
Cost of heating warm water |
1999 |
6/2003 |
Oil consumption {liters} |
approx. 37 |
23.5 |
Burner activations/month |
115 |
29 |
Monthly cost {euro} |
7.4 (@ 20 cts/liter) |
7.99 (@ 34 cts/liter) |
Annual cost {euro} |
88.8 |
95.88 |
Specific work {kWh/(m˛*a)} |
20.0 |
12.33 |
These data are valid at an A/V - factor of 0.74, heated area: 222m², fuel heating oil. Washing machine and dish-washer are also connected.
The mean consumption of 12.33 kWh/(m˛*a) also meets the German EnEV (Energy-Saving Regulation): 12.5 kWh/(m˛*a).
Who still thinks that a solar panel system can top that?
[ Contents ]
The future
Look at the graph showing column #10 of the overview table of normalized oil consumption. It is clear that optimization on the basis of current components is complete. Annual consumption will remain between 8.8 and 8.9 liters/m˛ according to patterns of use. (That is near the low-energy house limit: 8 liters/m˛a for heating only with no hot water!)
Further savings can only be achieved by structural modifications, such as installation of new windows of better k-number or a new boiler:
|
|
- Windows are very expensive and if you already have double-glazing you need to calculate sharply.
- A new boiler would only save energy in combination with a modulating burner from 3-10 kW, but that would cost you the earth.
[ Contents ]
Deeper background information
- Heating operation
Up-to-date heating operation graphs and statistics since 1995.
- Heating Log
Some graphs and figures to do with running a heating system.
- See what maintenance can do
- Savings when heating
How to read the consumption figures the right way?
- Technical Terms for heating technology and statistic.
|